Natural Soil Products – Tremont, Pennsylvania, USA
Ownership: Natural Soil Products
Location: Tremont, Pennsylvania, USA
Construction: Phase 1 Complete / Phase 2 Complete
Product: SG BUNKER® System with GORE® Cover
Input Quantity: 200,000 tons per year of Biosolids
No. of Heaps: 18 Bunkers, 18 covers, 164ft x 27 ft x 11.5 ft each
Treatment Time: Primary Phase for 18 – 21 days
Aeration: In-ground Trenches
Control Parameters: Programmable Interval Mode
Input Material: Dewatered Sludge Biosolids
Equipment: Windrow Turner, Front End Loader, Mobile Screening
End Product: Agricultural Grade Soil Amendment
Project Overview
In 2022, Natural Soil Products (NSP) experienced significant odor issues at its open-windrow biosolids composting facility. The strong odors from the windrow operation were causing complaints from the surrounding community and heightened scrutiny from regulators. Faced with pressure to mitigate odors and environmental impacts, NSP began searching for a more controlled composting solution that could reduce odors, manage leachate, and ensure regulatory compliance. The goal was to upgrade from the basic open windrow method, which offered limited control over emissions and moisture, to a technology that could increase process control and contain odors.
After evaluating options, NSP engaged Sustainable Generation, LLC (SG) to help identify a proven odor-reducing composting technology. SG ADVANCED COMPOSTING™ Technology – the SG BUNKER® System with GORE® Cover – was selected for a pilot test due to its track record of dramatically reducing odors (by over 90% in similar projects), meeting EPA 503 regulations for pathogen reduction and vector attraction reduction, and improving overall environmental control. This covered, aerated static pile technology was designed to address the site’s challenges, including odor mitigation, leachate management, vector control, and compliance with stringent Pennsylvania Department of Environmental Protection (DEP) regulations. With odor reduction being the most pressing issue, NSP and SG launched a pilot demonstration in 2022 to validate that this system could meet the facility’s needs and outperform the existing windrow process.
Pilot Study
In 2022, NSP’s pilot demonstration project utilized a single SG MOBILE® System (a mobile version of the covered aerated static pile) with a GORE® Cover to compost biosolids on a trial basis. Within days of setup, the pilot unit was operational, composting a blend of biosolids and bulking agents under the protective cover. Multiple batches were run over the pilot period to evaluate key performance metrics, including odor mitigation, leachate and moisture control, vector (pest) control, and final compost quality. The pilot also aimed to confirm that the process could meet or exceed all local and state regulatory requirements, such as pathogen reduction standards, while determining the optimal recipe and cycle time for NSP’s materials. This side-by-side evaluation against the traditional windrow method allowed NSP and regulators to compare environmental impacts and compost results directly.
Pilot Demonstration Results: The pilot study confirmed the effectiveness of the SG-covered composting system on all objectives:
- Odor Reduction: Dramatic decrease in odor emissions compared to the open windrow process (virtually eliminating off-site odor). The covered, aerated static pile system demonstrated significantly lower odor levels, validating the technology’s ability to control odors.
- Leachate & Moisture Control: The GORE® Cover prevented rainwater infiltration and excess evaporation, significantly reducing leachate generation and enabling better moisture retention in the composting mass. This ensured stormwater was kept separate from the compost, simplifying leachate management and environmental compliance.
- Regulatory Compliance: The process consistently met PFRP (Process to Further Reduce Pathogens) requirements, reaching required temperatures (≥131°F for 3+ days) to sanitize the biosolids. All local and state regulatory standards for odor and pathogen control were satisfied or exceeded, demonstrating the system’s compliance readiness.
- Compost Quality: The finished compost from the pilot was stable, mature, and of high quality, suitable for agricultural use. Nutrient-rich, Exceptional Class A compost was produced, confirming that a single-phase process can yield an agriculture-grade end product.
These outcomes of the pilot project gave NSP complete confidence in SG ADVANCED COMPOSTING™ Technology. The pilot demonstrated that the SG system could outperform the windrow operation, all while mitigating odors and leachate issues. This successful demonstration proved the feasibility of scaling up the covered aerated static pile solution. Based on the pilot results, particularly the significant odor reduction, NSP proceeded with plans to implement a full-scale SG Bunker System at the facility.
Left to right: SG MOBILE® System Pilot, Construction phase, SG BUNKER® System full-scale implementation
Full-Scale Implementation
With the pilot a success, NSP took quick action with odor mitigation measures. They chose an accelerated timeline to deploy the full-scale covered composting system. In early 2023, immediately following the pilot, NSP and SG began implementing an 18-bunker SG BUNKER® System at the Tremont site as a long-term solution to the odor and environmental challenges.
The SG team expedited the manufacturing and delivery of all system components for the 18 bunkers, leveraging their experience to meet the aggressive timeline. Rapid production and mobilization enabled NSP to commence site construction without delay. Remarkably, the entire project – from final design and site work to construction and commissioning – was completed in under one year. By late 2023, the new covered composting facility was fully operational. The final installation consists of 18 concrete bunkers equipped with in-floor aeration and covered by GORE® Covers, processing biosolids on a footprint of less than 3 acres.
Once the full-scale SG BUNKER® System went live, NSP quickly demonstrated that it could meet all the performance criteria set by regulators. Odors at the site were brought under control, leachate was managed within the new system’s infrastructure, and compost production continued at the required throughput without issue. NSP successfully operated the new system in compliance with the PADEP Regulations, validating that the SG ADVANCED COMPOSTING™ Technology achieved the intended odor mitigation and environmental protection goals. The surrounding community and regulators noted the marked improvement in site conditions.
Contact Us
Our Blog
Projects, Technology, and News
Explore our blog to discover more about our projects, technology advancements, and exciting news.
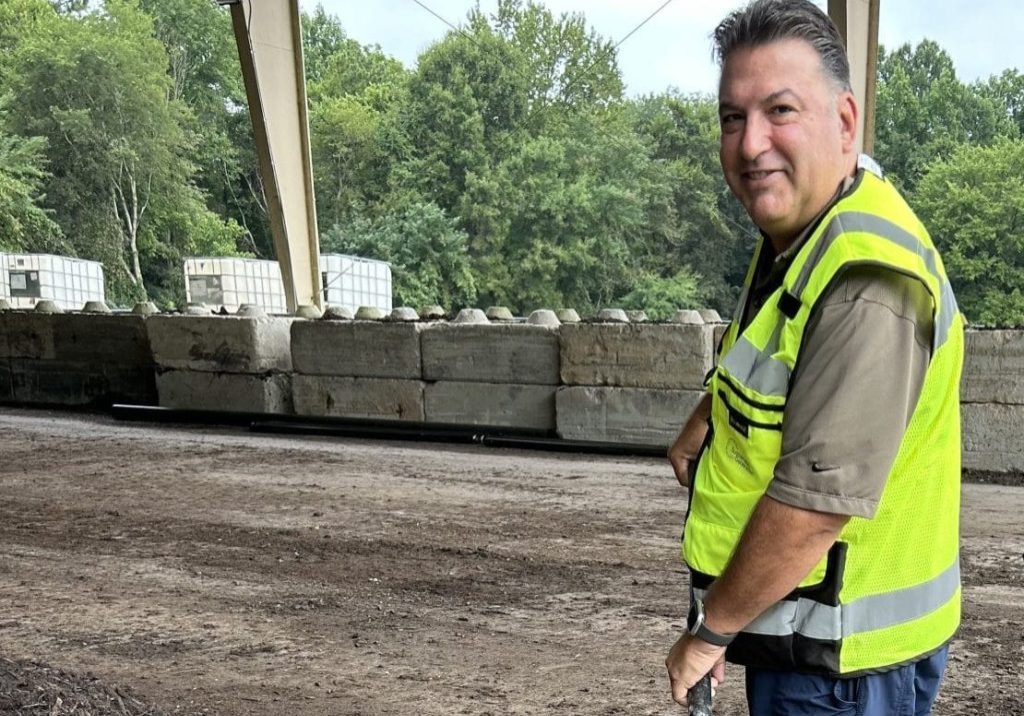
INTERVIEW WITH A BIOSOLIDS EXPERT
Biosolids expert Dan Collins, P.E., shares insights on safe, efficient composting.
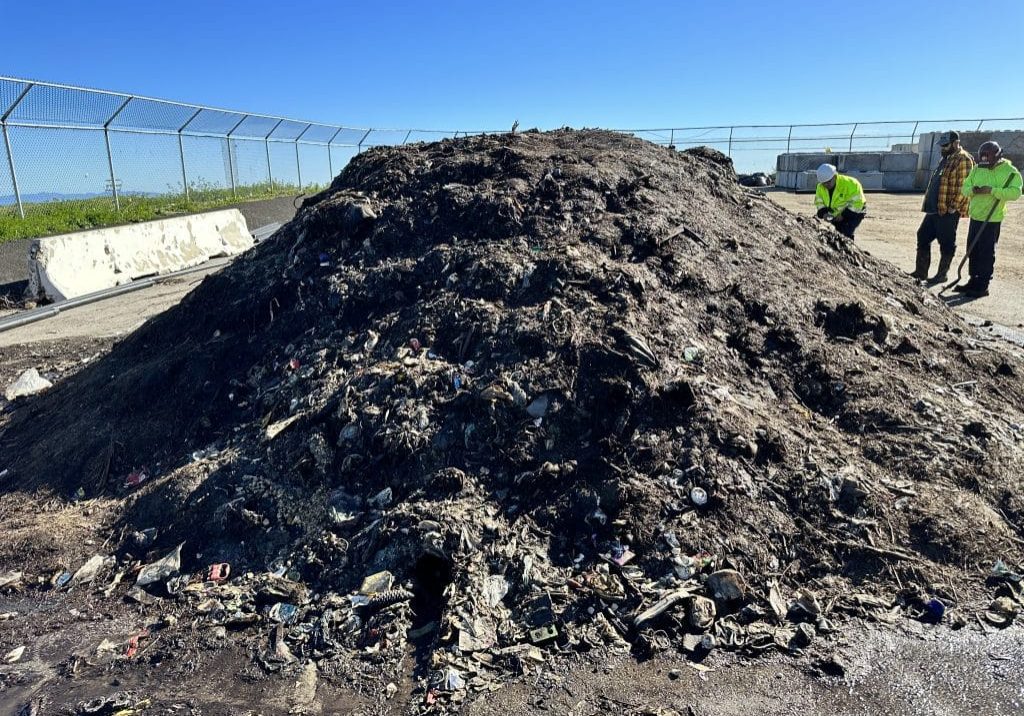
Summary of Performance GORE® Cover and Negative ASP
GORE® Cover was evaluated to quantify the performance versus an existing negatively aerated static
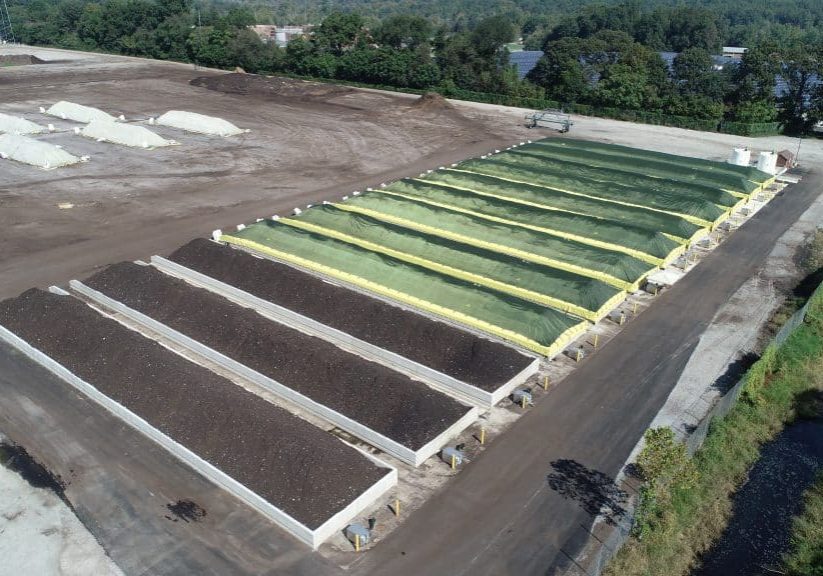
Composting Facility Delivers Significant Environmental Protection
The East Coast’s largest food waste composting site processes 57,000 tons of organics annually.
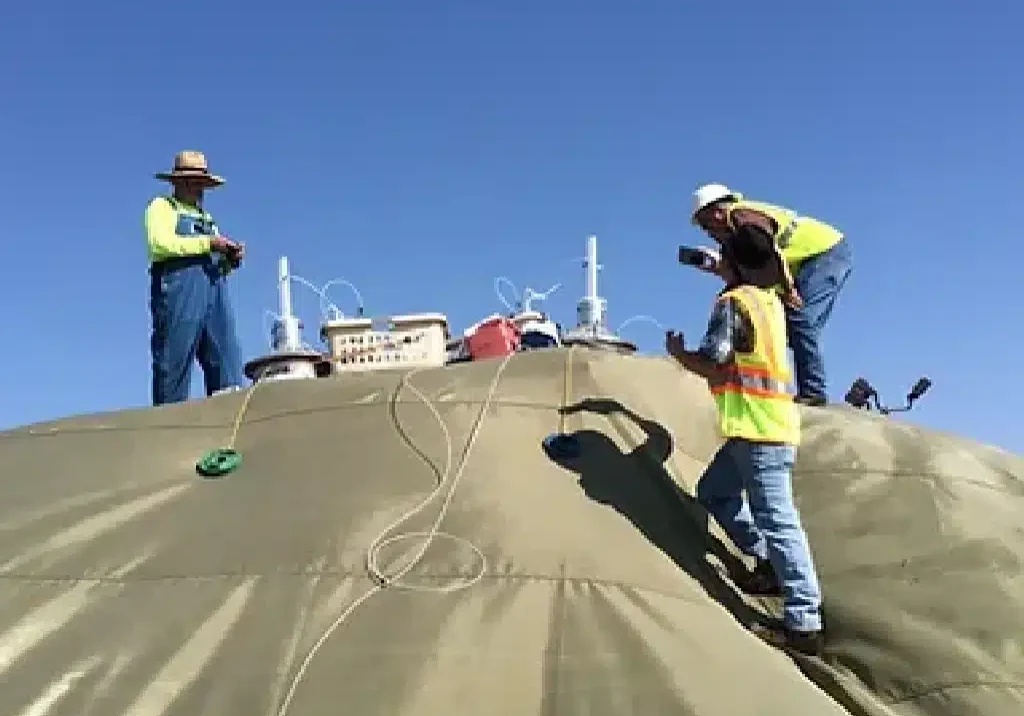
Exceeding Air Quality VOC Emission Regulatory Compliance in California
SG systems consistently meet and exceed California air quality regulations.

Positive ASP Composting: the Future of Organics
Two of the biggest issues faced by commercial composting operators are emissions (odor and
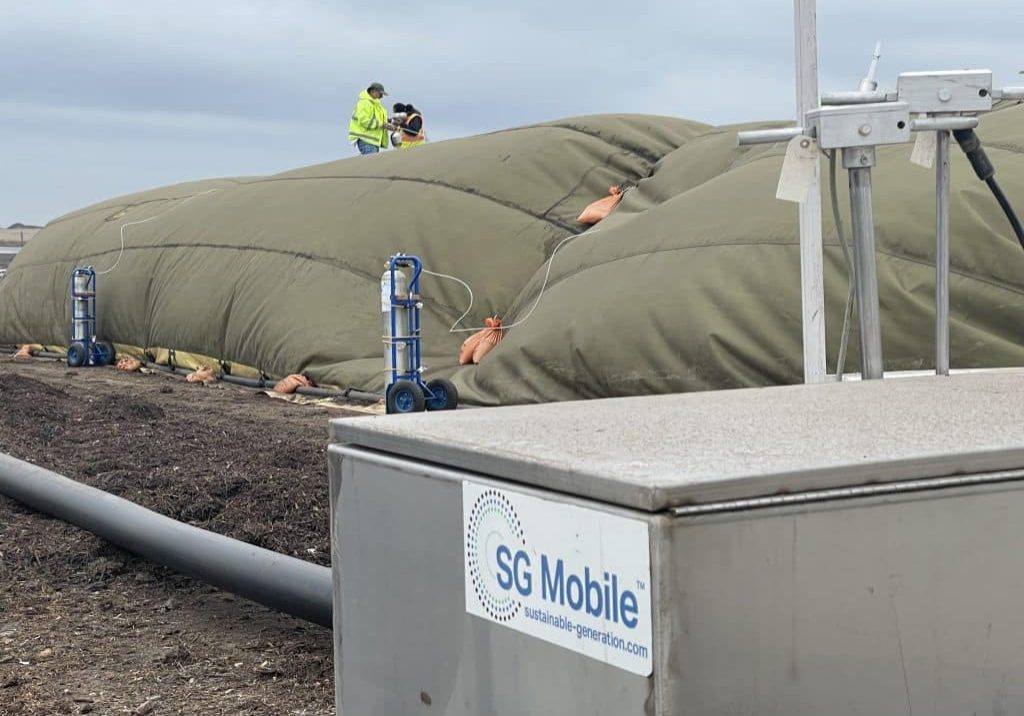
Proven Results: Over 20 Years Reducing Odors and Emissions in California
Sustainable Generation, LLC and the GORE® Cover have a long track record of success.
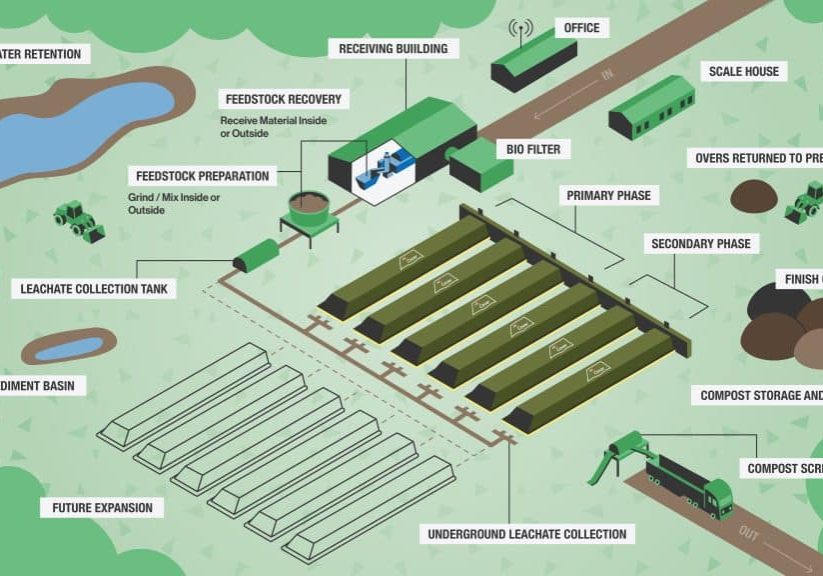
Why Smart Composting Facility Operators Keep Stormwater and Leachate Separate
During heavy storms, composting facilities face increased runoff and leachate.