Scaling to Meet Expanded Organics Diversion Programs in Ontario
All Treat Farms, operated by Walker Environmental Group Inc., has processed yard waste, SSO, and AD Digestate at its Arthur Compost site for more than 15 years using a 32 SG BUNKER@ System with GORE® Cover. In 2021, as a result of an expanded organics diversion program in the region, Walker All Treat Farms needed to increase capacity without increasing the footprint of the facility.
PROJECT DETAILS
Site Name: Walker All Treat Farms
Ownership: Walker Environmental Group, Inc.
Location: Arthur, Ontario, Canada
Start-Up Date: December 2022
Product: SG BUNKER® System
Input Quantity: 100,000 M-Tons per year expansion, 200,000 total capacity
No. of Heaps: 32 heaps, 32 covers, 50m x 8m x 3.7m each
Treatment Time: 8 weeks/batch in 3 phases:
Phase 1 (covered): 4 weeks
Phase 2 (covered): 2 weeks
Phase 3 (uncovered): 2 weeks
Aeration: In-Ground Trenching
Control Parameters: Oxygen Control Mode
Input Material: Source Separated Organics, AD Digestate, Yard & Green Waste
Equipment: a) Pre-Treatment (Grinders)
b) Front-end loaders
c) Trommel Screen
d) Water Truck
End Product: High-Quality Finished Compost sold under the All Treat Farms brand name
THE SG SOLUTION
Meeting Requirements While Producing High-Quality Compost
To maximize the All Treat Farms’ capacity within the existing footprint, an upgrade to a 32 SG BUNKER® System was decidedly the best choice. Featuring SG COMPOST CONTROL™ System, the facility will process the expanded feedstock quantity while continuing to meet environmental regulations.
Of significant importance to the All Treat Farms project was the SG BUNKER® System’s capability to comply with the state and local regulatory requirements and resource efficiency:
1. Meeting air quality standards for Odor control
2. Meeting Vector Attraction Reduction (VAR) requirements;
3. Meet Time and Temperature requirements (PFRP) for pathogen reduction
4. Produce high-quality finished compost
5. Clear Separation of Leachate from Stormwater
6. Low Power Consumption
7. Moisture Management
8. Lowest Total Cost of Ownership over the life of the facility
PROJECT GALLERY
SG BUNKER® System at the Walker All Treat Farms Compost Facility
- Thermal of All Treat Farms in the dead of winter.
RESULTS DELIVERED
A Sustainable Solution with True Scale
Construction for the project is complete, and the compost site is currently operational.
Contact Us
Our Blog
Projects, Technology, and News
Explore our blog to discover more about our projects, technology advancements, and exciting news.
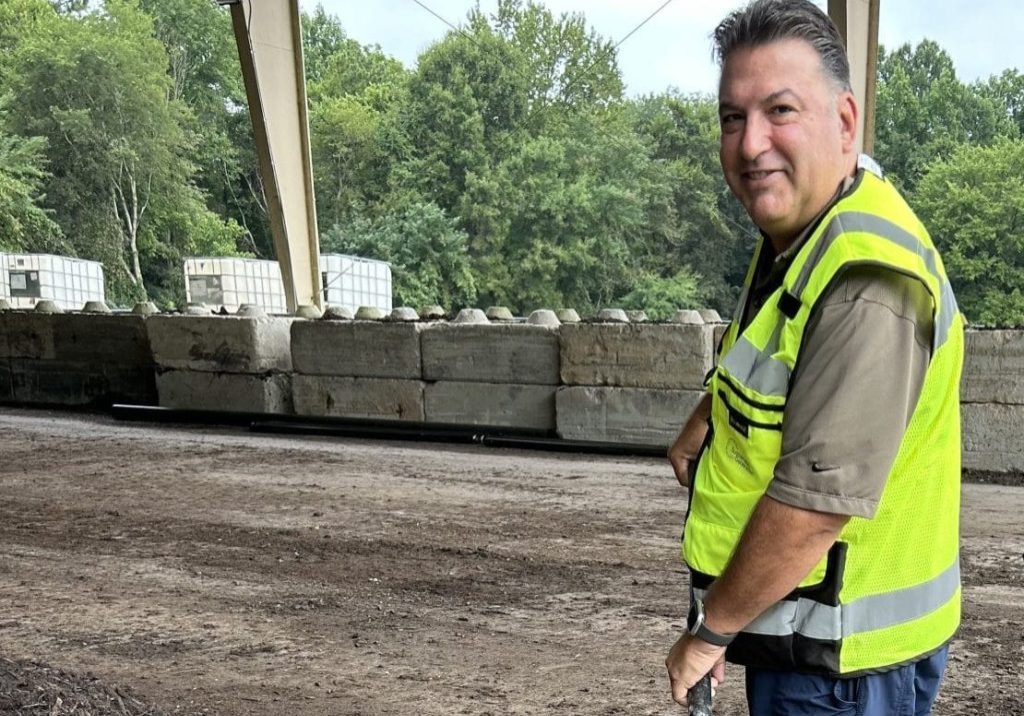
INTERVIEW WITH A BIOSOLIDS EXPERT
Biosolids expert Dan Collins, P.E., shares insights on safe, efficient composting.
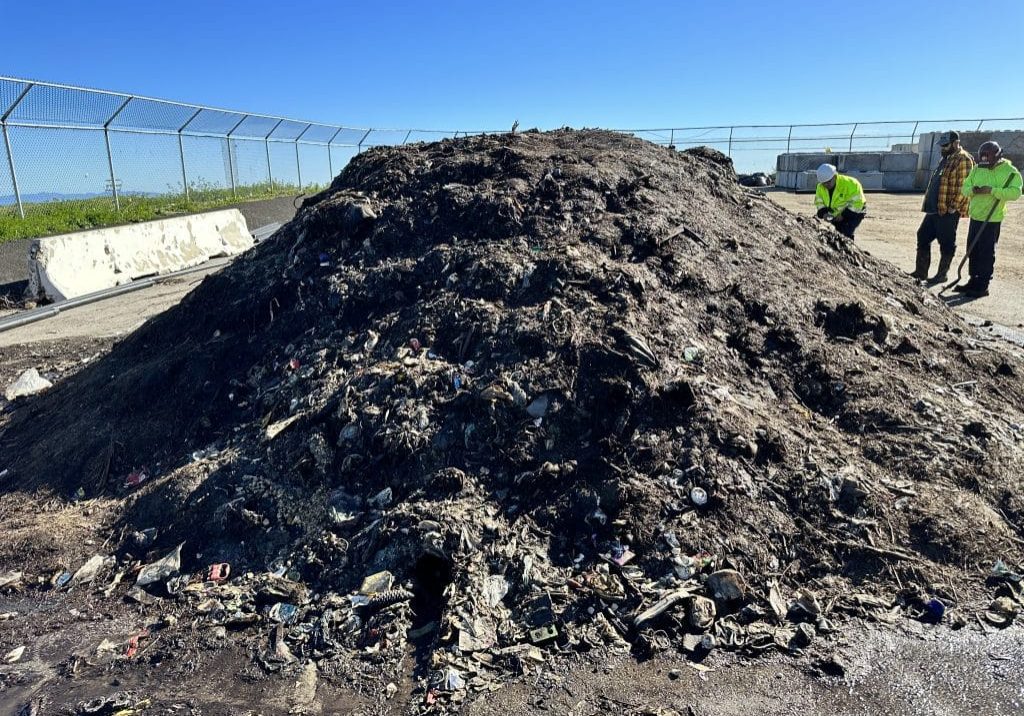
Summary of Performance GORE® Cover and Negative ASP
GORE® Cover was evaluated to quantify the performance versus an existing negatively aerated static
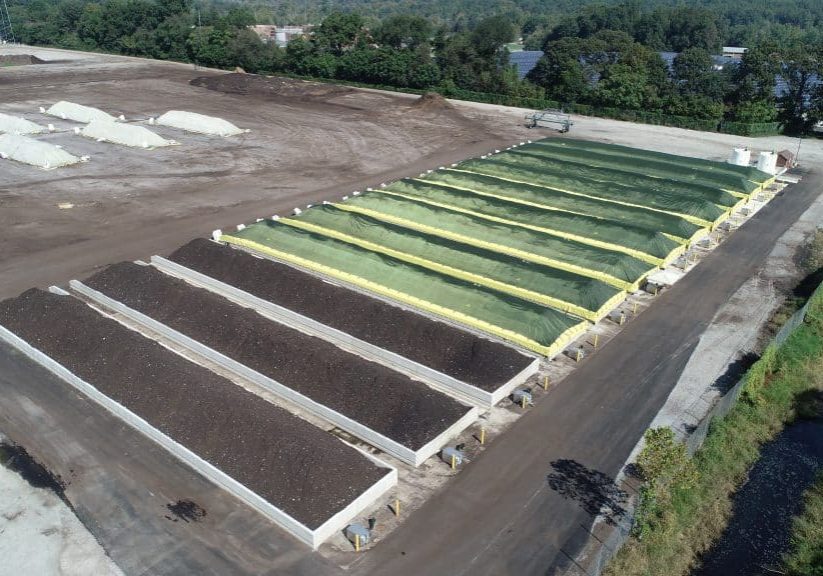
Composting Facility Delivers Significant Environmental Protection
The East Coast’s largest food waste composting site processes 57,000 tons of organics annually.
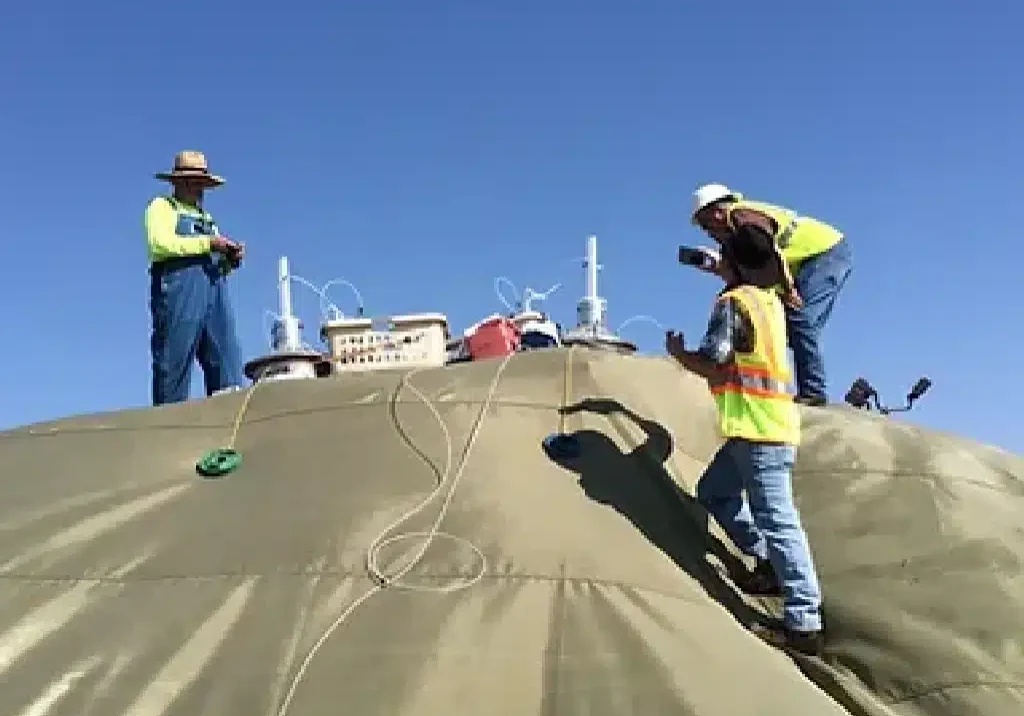
Exceeding Air Quality VOC Emission Regulatory Compliance in California
SG systems consistently meet and exceed California air quality regulations.

Positive ASP Composting: the Future of Organics
Two of the biggest issues faced by commercial composting operators are emissions (odor and
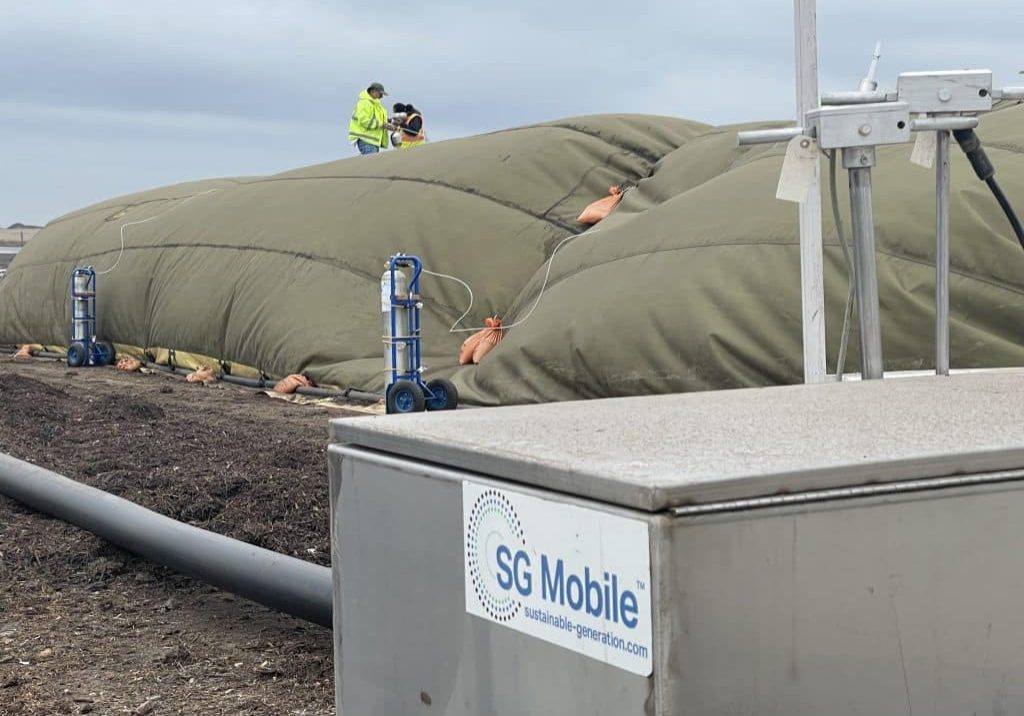
Proven Results: Over 20 Years Reducing Odors and Emissions in California
Sustainable Generation, LLC and the GORE® Cover have a long track record of success.
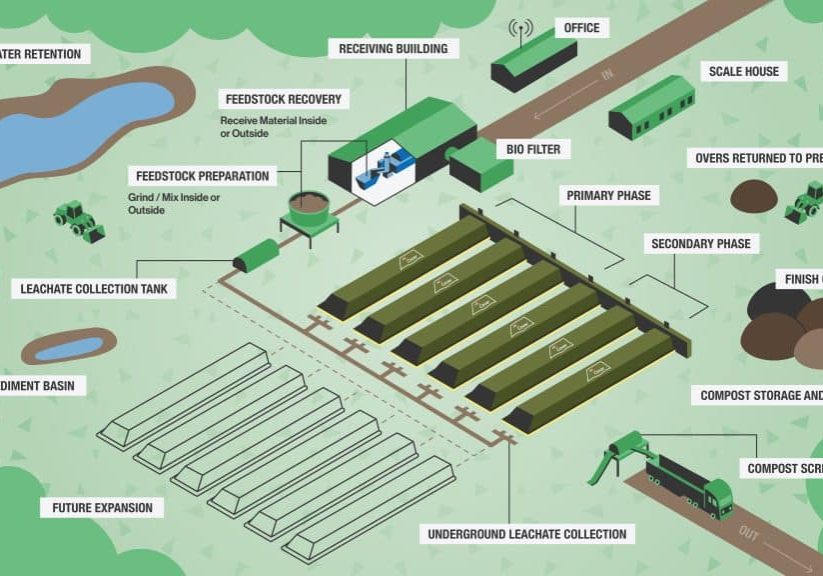
Why Smart Composting Facility Operators Keep Stormwater and Leachate Separate
During heavy storms, composting facilities face increased runoff and leachate.